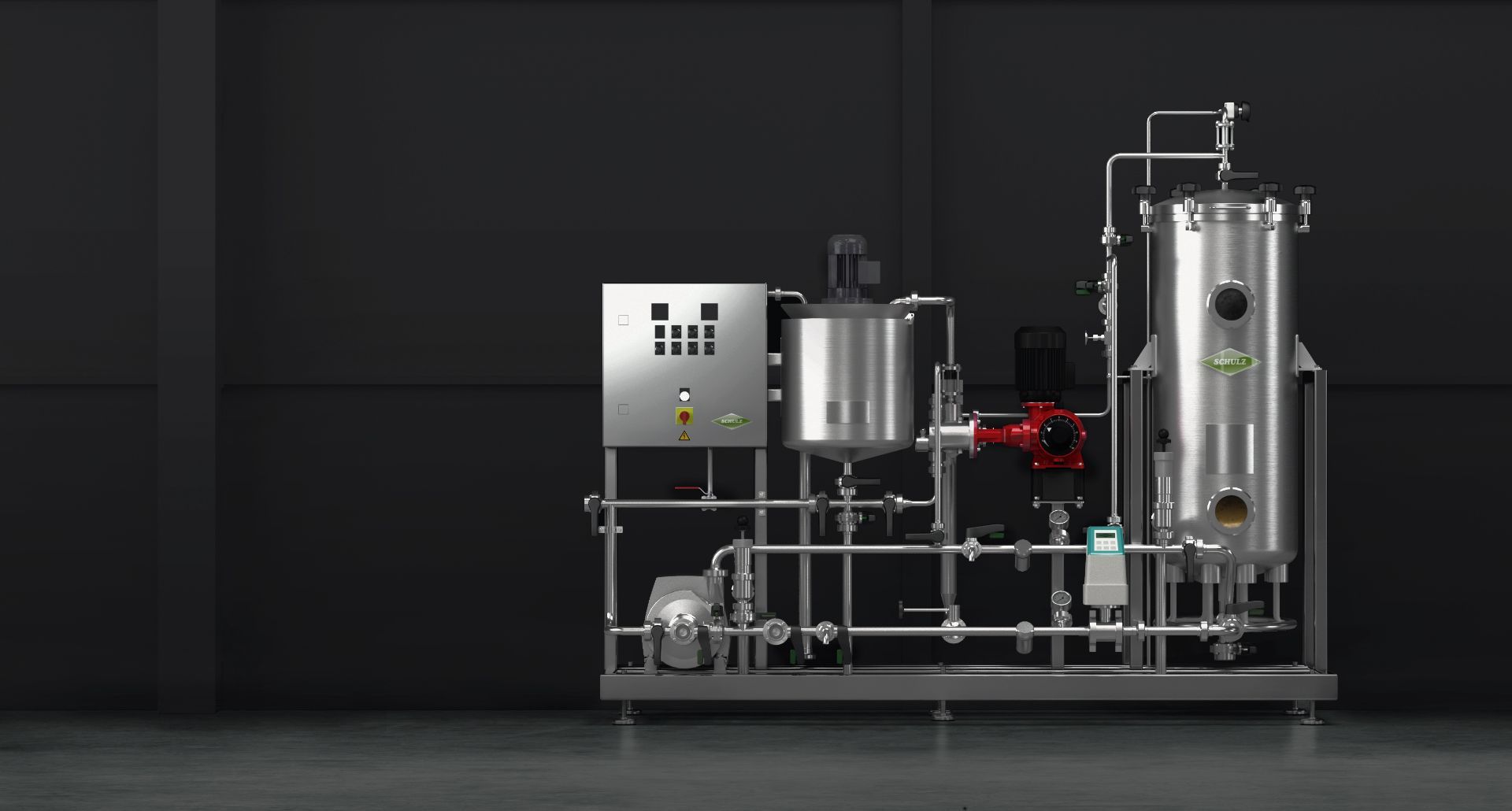
Plant technology & expansions
The most innovative system supplier for turnkey brewing and malting plants, distilleries and special vessels.
Instructions
& guides
Brewhouse systems
Systems for cold applications
Automation
Raw material refinement
Pioneer Pro
Since the 1970s, SCHULZ has been involved in the automation of brewery plants. A glance at the beginnings shows how rapidly this product line developed. From the contactor control system and the crossbar distributor to the introduction of the world's first brewhouse automation system based on a microprocessor in the 1980s, the company Peter Bischof, a permanent partner of KASPAR SCHULZ, was a cutting-edge pioneer. For the first time ever, complex control tasks were managed in a brewhouse using a structure called a step sequence. Terms that we take for granted today, such as recipe, variety and switching criterion, were developed back then. The application, established as the Bischof controller, was upgraded with a visualisation screen in the 1990s. Hierarchical password protection, recipe management, a line recorder, and a database connection were introduced in the 2000s.
Nowadays, all this is taken for granted. Current requirements aim at designing systems intelligently. Aspects such as batch tracing, maintenance management and cloud integration are often discussed, but are not always implemented in mid-sized companies. SCHULZ took this as an opportunity to meet these challenges with its own system. The establishment of an automation department at the Bamberg site has been in development for several years and is now making its debut with the market launch of the SCHULZ Pioneer Pro.
The focus is on the conversion of the numerous Bischof systems. Supporting the tried-and-tested systems goes hand in hand with transforming these once-pioneering systems to keep up with the new digital era.
Facts:
- Web-based structure for operation via mobile devices
- Industrial PC as a visualisation computer without rotating parts
- Latest-generation Siemens S7-1500 control unit
- Decentralised peripherals allow for short wiring routes and easy expansion
- Components connected via ProfiNet
- Intelligent process control through process engineering optimisation of recipes
- Database-supported, scalable system with latest web technology and communication protocols to comply with the Industry 4.0 standard
- Alarm management with product-oriented documentation for optimum support in case of malfunctions
- Simple recipe creation in Excel style via web browser
- Customer-specific hierarchical access management
- Article and goods receipt management for resource accounting and batch tracing
- Maintenance management with cloud connection to central SCHULZ services
Expand your production possibilities
using our system solutions
KASPAR SCHULZ is the only company in the world in the field of brewing, malting and distilling to offer its customers a full-service package with the best quality in these three segments from a single source.
A multitude of innovations, patents and technical masterpieces are combined in the huge and diverse product range. As the oldest brewery machine manufacturer in the world, we are bringing tradition into the future. Expertise accumulated over three centuries flows into the continuous improvement of our technology and products.
Bucking the growing trend towards outsourcing, we still prefer to do everything ourselves – gladly and highly successfully, at that. If SCHULZ is on the label, the product is an original SCHULZ made entirely in Bamberg from the first production step to plant commissioning.